Effect of bagging with four types of bags on fruit quality of different varieties of pears
-
摘要: 探讨了4 种类型果袋对5 个梨品种果实质量、外观和品质的影响。结果表明, 黄花梨果实质量以单层黄袋为最大, 新世纪则以双层黑袋为最重。果袋类型对不同品种果实外观有明显效应。套用双层果袋果面黄白色, 色泽一致, 光洁, 果点不明显, 同时果皮厚度和果肉石细胞数量有所减少, 果肉含水量略有增加, 糖酸比发生变化。梨果实采用新型果袋套袋,经济效益显著提高, 达到高投入高产出的要求。表3 参2Abstract: Effects of bagging with 4 types of bags on fruit weight , appearance and quality of 5 varieties of pears are discussed here .It's indicated that fruit weight is largest in Yellow Flower Pear covered with a single-layered yellow bag , while in Shinseiki the heaviest fruit is that bagged with a double-layered black bag .Types of bags obviously affect the fruit appearance of different varieties .The fruit covered with a double-layered bag is uniformly yellowwhite in color and smooth in skin , with no apparent macula .Meanwhile , there are a reduction in skin thickness and quantity of stone cells of flesh and a slight increase inmoisture content of the flesh .The ratio of sugars to acids also changes .As a result , economic effects increase , which meets the requirement of a high quality reward resulting from a high input .
-
Key words:
- pears /
- fruits /
- bagging /
- fruit quality
-
以木材为原料的胶合板易受虫菌侵害而腐朽[1],使胶合板的使用受到限制。经过防腐处理的胶合板,可有效解决上述问题,达到防腐、防虫、防霉的效果,延长胶合板的使用期限。但是经过防腐处理,会降低胶黏剂与木材表面的润湿性[2],防腐剂的某些成分会与胶黏剂相互作用[3-5],导致胶合强度下降,影响最终制品的性能。因此,研究防腐胶合板的制作工艺对实际生产和开发新产品具有重要的意义。响应面法可以对多个因素与多个响应值之间的函数关系进行二次回归方程拟合,优化得出最佳工艺参数[6]。本研究在前期探索性试验的基础上,拟以硼砂、乙二醛、丙三醇复配物为防腐剂,酚醛树脂胶为胶黏剂,制作杨木防腐胶合板,以板的胶合强度及硼保持率为响应值,应用响应面法优化杨木防腐胶合板的制作工艺,以期得到胶合强度和硼保持率均较高的杨木防腐胶合板最佳制作工艺参数。
1. 材料和方法
1.1 材料与试剂
杨木单板,含水率10%~12%,规格为300 mm × 140 mm × 1.2 mm,建阳胶合板厂;苯酚、氢氧化钠、硼酸、丙三醇均为分析纯:天津市福晨化学试剂厂;甲醛(37%水溶液,质量分数)、乙二醛(40%水溶液,质量分数)为分析纯:西陇化工股份有限公司;彩绒革盖菌Coriolus versicolor,中国林业科学研究院森林保护研究所。
1.2 试验方法
1.2.1 酚醛树脂胶的制备与性能
酚醛树脂胶制备工艺为:苯酚∶甲醛水溶液∶氢氧化钠(30%水溶液,质量分数)的摩尔比为1.0∶2.0∶0.5。控制水温在50 ℃左右,将溶化的苯酚加入三口烧瓶后开动搅拌器,依次加入氢氧化钠溶液和第1次甲醛溶液;待放热反应停止后,再缓慢加热升温至(90±2) ℃,保温15 min;降温至80 ℃,加入第2次甲醛溶液,升温升至(90±2) ℃,保温20 min后开始测黏度;当黏度达到要求后,降温至35 ℃以下放料。
基本参数:pH 11.37;游离醛0.086% ;黏度(涂4杯)42.44 s/ 23 ℃;固含量50%;固化时间42.52 min。
1.2.2 防腐液的配置
用硼砂、乙二醛、丙三醇和蒸馏水调配防腐液,配比见表 1。
表 1 3种防腐液中各组分的配比Table 1. Component ratio of the 3 kinds of preservative solutions编号 硼砂质量分数/% 乙二醛质量分数/% 丙三醇质量分数/% 1 6 2 1 2 6 3 1 3 6 4 1 1.2.3 单板防腐处理
为了便于防腐液渗透,将杨木单板放入80 ℃烘箱中干燥3 h,再浸入防腐液中2 h。浸渍完毕后,取出单板,沥干,根据实验方案,分别放在65,70,75 ℃烘箱中分别干燥4,5,6 h,封存2 d,备用。
1.2.4 胶合板制作及胶合强度测试
以酚醛树脂胶为胶黏剂,将防腐处理后的杨木单板按相邻层纤维方向垂直进行组坯,压制成3层胶合板。涂胶量280 g·m-2(双面)。热压工艺为热压温度140 ℃,热压时间1.0 min·mm-1,单位压力1.0 MPa。胶合强度检测依据国家标准GB/T9846-2004中Ⅰ类胶合板和GB/T 17657-1999中4.15.4.2a中规定的快速检验法。
1.2.5 流失实验
按照木材防腐行业标准LYT 1283-2011《木材防腐剂对腐朽菌毒性实验室试验方法》中的水溶性防腐剂流失实验进行。
1.2.6 硼保持率的测定
硼保持率的测定方法参照文献[7]。
1.2.7 最佳工艺条件制作的杨木防腐胶合板室内耐腐性能检测
参照国家标准GB/T 13942.1-2009《木材耐久性能 第1部分:天然耐腐性实验室试验方法》和林业行业标准LY/T 1283-2011《木材防腐剂对腐朽菌毒性实验室试验方法》进行试验,并计算试样的质量损失率,评价耐腐性等级。
1.2.8 试验设计与数据处理方法
采用Design-Expert 8.0.5中Box-Behnken设计模式进行试验设计与数据分析。以防腐液中乙二醛的质量分数、干燥温度、干燥时间3个因子为自变量,分别用x1,x2,x3表示,在探索性试验的基础上,确定各影响因素合适的条件范围,分别为2%~4%,65~75 ℃,4~6 h,以杨木防腐胶合板的胶合强度y1和硼保持率y2作为响应值,试验自变量因素编码及水平见表 2。
表 2 试验自变量因素编码及水平Table 2. Code and level of factors chosen for the trial水平 x1防腐液中乙二醛的质量分数/% x2干燥温度/% x3干燥时间/h -1 2 65 4 0 3 70 5 1 4 75 6 2. 结果与分析
2.1 Box-Benhnken 的中心组合设计试验
杨木防腐胶合板胶合强度y1及硼保持率y2试验设计与结果见表 3。
表 3 试验设计与结果Table 3. Experimental designs and results试验号 x1 x2 x3 单板含水率/% y1胶合强度/MPa y2硼保持率/% 1 0(3) 1(75) 1(6) 4-83 1-27 43-142 5 2 0(3) -1(65) -1(4) 6-45 1-30 48-880 6 3 -1(2) -1(65) 0(5) 6-09 1-39 43-259 5 4 0(3) 0(70) 0(5) 5-83 1-48 52-597 9 5 1(4) 1(75) 0(5) 5-42 1-44 39-040 4 6 -1(2) 0(70) 1(6) 4-93 1-23 40-222 2 7 -1(2) 1(75) 0(5) 5-42 1-28 39.104 4 8 0(3) 0(70) 0(5) 5-81 1-43 51.897 9 9 0(3) -1(65) 1(6) 5-08 1-32 48-005 9 10 0(3) 0(70) 0(5) 5-89 1-44 49-097 9 11 0(3) 0(70) 0(5) 5-88 1-42 49-077 8 12 0(3) 1(75) -1(4) 5-99 1-35 48-849 2 13 0(3) 0(70) 0(5) 5-91 1-43 50-099 7 14 -1(2) 0(70) -1(4) 6-31 1-33 40-292 8 15 1(4) -1(65) 0(5) 5-52 1-27 30-673 3 16 1(4) 0(70) -1(4) 6-38 1-36 38-571 8 17 1(4) 0(70) 1(6) 4-92 1-42 38.021 5 说明:未流失试件中硼(以B2O3计)为4.9~5.2kg·m-3。 采用Design-Expert 8.0.5软件对所得数据进行二次回归分析,3个因素经过拟合得到胶合强度y1及硼保持率y2回归方程如下所示:
$\begin{align} & {{y}_{1}}=-10.735\text{ }00-0.937\text{ }50{{x}_{1}}+0.320\text{ }50~{{x}_{2}}+0.917\text{ }50~{{x}_{3}}+ \\ & 0.014\text{ }00~{{x}_{1}}~{{x}_{2}}+0.040\text{ }00~{{x}_{1}}~{{x}_{3}}~-0.005\text{ }00~{{x}_{2}}~{{x}_{3}}- \\ & 0.035\text{ }00{{x}_{1}}^{2}-0.002\text{ }40~{{x}_{2}}^{2}-0.070\text{ }00{{x}_{3}}^{2};~ \\ & {{y}_{2}}=-460.573\text{ }72+16.132\text{ }32x1+12.171\text{ }25x2+26.756\text{ }50{{x}_{3}}+ \\ & 0.626\text{ }11~{{x}_{1}}{{x}_{2}}-0.119\text{ }92~{{x}_{1}}~{{x}_{3}}~-0.241\text{ }60~{{x}_{2}}~{{x}_{3}}-10.238\text{ }65~{{x}_{1}}^{2}- \\ & 0.091\text{ }85~{{x}_{2}}^{2}-1.038\text{ }50~{{x}_{3}}^{2}。 \\ \end{align}$
这2个模型的R2值分别为0.925 6和0.942 8,接近于1,说明通过二次回归得到的杨木防腐胶合板胶合强度及硼保持率的模型与试验拟合较好。
2.2 影响防腐胶合板胶合强度的主要因素分析
杨木防腐胶合板胶合强度y1回归模型方差分析结果见表 4。表 4可以看出:方程y1的P=0.003 4<0.01极显著,失拟项P=0.176 0>0.05不显著,说明所建立的回归二次模型成立。方程y1中x1 x2,x22,x32对响应值胶合强度影响极显著,x1,x1 x3对响应值胶合强度影响显著,x2,x3,x2 x3,x12对响应值胶合强度影响不显著。影响杨木防腐胶合板胶合强度的主次因素依次为x1>x3>x2,即防腐液中乙二醛的质量分数>干燥时间>干燥温度。
表 4 胶合强度回归模型方差分析Table 4. Analysis of variance for regression equation of the bonding strength项目 平方和 自由度 均方 F值 P值 显著性 模型 0.083 956 9 0.009 328 9.673 929 0.003 4 ** x1 0.008 450 1 0.008 450 8.762 963 0.021 1 * x2 0.000 450 1 0.000 450 0.466 667 0.516 5 x3 0.001 250 1 0.001 250 1.296 296 0.292 4 x1 x2 0.019 600 1 0.019 600 20.325 930 0.002 8 ** x1 x3 0.006 400 1 0.006 400 6.637 037 0.036 7 * x2 x3 0.002 500 1 0.002 500 2.592 593 0.151 4 x12 0.005 158 1 0.005 158 5.348 928 0.054 0 x22 0.015 158 1 0.015 158 15.719 300 0.005 4 ** x32 0.020 632 1 0.020 632 21.395 710 0.002 4 ** 残差 0.006 750 7 0.000 964 失拟项 0.004 550 3 0.001 517 2.757 576 0.176 0 净误差 0.002 200 4 0.000 550 总误差 0.090 706 16 说明:*差异显著,P<0.05;**差异极显著,P<0.01 根据拟合模型y1绘制胶合强度响应曲面图(图 1~3)。图 1为干燥时间在0水平,即在固定干燥时间5 h的条件下,防腐液中乙二醛的质量分数和干燥温度的响应曲面和等高线。由图 1可知,防腐液中乙二醛的质量分数与干燥温度的交互作用显著。当干燥时间一定时,随着干燥温度升高,胶合强度提高,干燥温度为75 ℃时,胶合强度达最大值;当干燥时间一定,干燥温度为75 ℃时,随着防腐液中乙二醛质量分数的增大,在试验范围,胶合强度呈上升趋势。因为较高的温度可以促进乙二醛、丙三醇、硼砂与木材之间反应生成聚缩醛网络[8],减弱硼砂与酚醛树脂胶之间的相互作用[3-5],避免酚醛胶凝胶[9],减小对胶合强度的不利影响。图 2为干燥温度在0水平,即在固定干燥温度70 ℃的条件下,防腐液中乙二醛的质量分数和干燥时间的响应曲面和等高线。由图 2可知:等高线图呈椭圆形,说明防腐液中乙二醛的质量分数和干燥时间两者交互作用较显著。随着防腐液中乙二醛质量分数的增大,胶合强度随之上升,乙二醛质量分数为4%时,胶合强度达到最大值。这可能是因为乙二醛分子中有2个相互连接的羰基,化学性质活泼,可以同时与木材、酚醛树脂胶发生化学反应[10-11],起到桥接作用,有利于酚醛树脂胶与木材之间形成化学键,提高胶合强度。图 3为防腐液中乙二醛的质量分数在0水平,即在固定防腐液中乙二醛质量分数为3% 的条件下,干燥温度与干燥时间的响应曲面和等高线。由图 3可知,干燥温度与干燥时间的交互作用较弱,防腐液中乙二醛的质量分数一定时,随着干燥时间的延长,胶合强度亦增大,约5 h时达到最大值,随后呈下降趋势。可能是由于随着干燥时间的延长,单板产生变形或翘曲,单板含水率太低,容易吸入胶粘剂,使胶接界面产生缺胶等现象,因而胶合强度降低[12]。
由Design-Exper软件分析杨木防腐胶合板胶合强度最佳工艺参数为防腐液中乙二醛质量分数4%,干燥温度73.14 ℃,干燥时间5.08 h,在此工艺条件下,胶合强度预测值可以达到1.46 MPa。
2.3 影响防腐胶合板硼保持率的主要因素分析
杨木防腐胶合板硼保持率y2回归模型方差分析结果见表 5。
表 5 硼保持率回归模型方差分析Table 5. Analysis of variance for regression equation of the retention rate of boron项目 平方和 自由度 均方 F值 P值 显著性 模型 574.040 10 9 63.782 24 12.822 20 0.001 4 ** xl 34.328 34 1 348328 34 6.901 06 0.034 1 * x2 0.058 28 1 0.058 28 0.011 72 0.916 8 x3 6.484 08 1 6.484 08 18303 50 0.291 1 x2 39.201 37 1 39.201 37 7.880 69 0.026 2 * x3 0.057 52 1 0.057 52 0.011 56 0.917 4 x2 x3 5.837 06 1 5.837 06 1.173 43 0.314 6 x12 441.389 60 1 441.389 60 88.732 95 < 0.000 1 ** x22 22.199 89 1 22.199 89 4.462 86 0.072 5 x32 4.541 01 1 4.541 01 0.912 88 0.371 2 残差 348820 51 7 4.974 36 失拟项 24.331 14 3 8.110 38 3.092 80 0.152 0 净误差 10.489 38 4 2.622 34 总误差 608.860 60 16 说明:*差异显著,P<0.05;**差异极显著,P<0.01 由表 5可以看出:方程y2的P=0.001 4<0.01极显著,失拟项P=0.152 0>0.05不显著,说明所建立的模型成立。方程y2中x12 对响应值硼保持率影响极显著,x1,x1x2对响应值硼保持率影响显著,x2,x3,x1x3,x2x3,x22,x32对响应值硼保持率影响不显著。影响杨木防腐胶合板硼保持率的主次因素依次为x1>x3>x2,即防腐液中乙二醛质量分数>干燥时间>干燥温度。
根据拟合模型y2绘制防腐胶合板硼保持率相应曲面图(图 4~6)。图 4表明:干燥温度低、防腐液中乙二醛的质量分数小时,硼保持率低;但干燥温度过高、防腐液中乙二醛的质量分数过大也会导致硼保持率下降。这可能是由于防腐木材在干燥过程中,防腐剂附着在导管壁上的纹孔周围,同时木材中的水分通过导管壁上的纹孔排出[13],而乙二醛沸点低、在较高温度下易蒸发,如果防腐液中乙二醛的质量分数过大、干燥温度过高,防腐剂可能来不及附着就随乙二醛蒸发和水分排出而沉积在木材的表层,容易造成流失,导致硼保持率下降。结合图 5和图 6可知,只有合适的干燥温度和干燥时间才有利于乙二醛、丙三醇、硼砂与木材反应形成聚缩醛网络,硼在木材中的保持率才能达到最大值。
由Design-Exper软件分析杨木防腐胶合板硼保持率最佳制作工艺参数为防腐液中乙二醛质量分数2.91%,干燥温度70.18 ℃,干燥时间4.55 h,杨木防腐胶合板硼保持率y2 预测值可以达到50.85%。
总而言之,3个试验因素对杨木防腐胶合板胶合强度及硼保持率响应值的影响均不是简单的线性关系,平方项对响应值也有很大的影响;防腐液中乙二醛质量分数无论是对胶合强度还是硼保持率均有着显著的影响。
2.4 杨木防腐胶合板制作工艺的优化
理想的防腐胶合板制作工艺应该使胶合板具有较高的胶合强度,同时还需保证板中具有较高的硼保持率。通过对胶合强度y1和硼保持率y2拟合方程的联合求解,得出胶合强度预测值为1.43 MPa,硼保持率预测值为50.63%的最佳优化结果,此时防腐液乙二醛的质量分数、干燥温度和干燥时间分别为3.01%,70.39 ℃,4.87 h。
根据最优工艺参数,取整数值:防腐液中乙二醛的质量分数3.00%,干燥温度70 ℃,干燥时间5 h,制作杨木防腐胶合板,重复5次试验,测定杨木防腐胶合板胶合强度和硼保持率,以验证响应面法的可行性。结果显示胶合强度的实测平均值为1.46 MPa;硼保持率实测平均值为49.38%。预测值与实测值相近,说明采用响应面法优化杨木防腐胶合板的制作工艺是可行的。
2.5 最佳工艺条件制作的杨木防腐胶合板室内耐腐性能检测结果
用最佳工艺条件制作杨木防腐胶合板,并进行室内耐腐试验,共制作6个试样进行平行试验,测试结果是平均质量损失率为2.98%<10%,达到强耐腐等级,说明所选的防腐剂和制作工艺切实可行。
3. 结论
本研究通过Box-Benhnken 的中心组合设计响应面法建立了杨木防腐胶合板胶合强度y1和硼保持率y2的拟合方程:y1=-10.735 00-0.937 50x1+0.320 50x2+0.917 50x3+0.014 00x1x2 + 0.040 00x1x3-0.005 00x2x3 -0.035 00x12-0.002 40x22 - 0.070 00x32;y2=-460.573 72 + 16.132 32x1 + 12.171 25x2+26.756 50x3+0.626 11x1x2-0.119 92x1x3-0.241 60x2x3-10.238 65x12 - 0.091 85x22-1.038 50x32。
对试验结果进行方差分析可知,在本试验范围内,影响杨木防腐胶合板的胶合强度和硼保持率的主次因素依次均为防腐液中乙二醛的质量分数>干燥时间>干燥温度。
对模型方程y1和y2联合求解,得杨木防腐胶合板胶合强度和硼保持率均较高的最佳制作工艺参数:防腐液中乙二醛的质量分数3.00%,干燥温度70 ℃,干燥时间5 h;胶合强度预测值1.43 MPa,硼保持率预测值50.63%。根据优化工艺进行5次重复试验,得平均胶合强度实测值1.46 MPa,平均硼保持率实测值49.38%,与预测值相近,说明响应面法优化杨木防腐胶合板的制作工艺是可行的。
杨木防腐胶合板室内耐腐试验质量损失率为2.98%<10%,达到强耐腐等级,说明本研究所选的防腐剂和制作工艺切实可行。
期刊类型引用(1)
1. 姬宁, 杨守禄, 李丹. 单板类人造板防腐研究概述. 林业科技开发. 2015(03): 7-10 . 百度学术
其他类型引用(0)
-
- 链接本文:
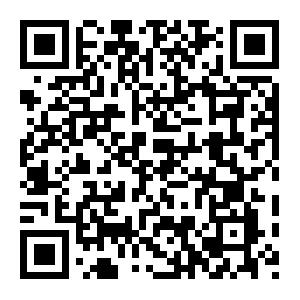
计量
- 文章访问数: 1414
- HTML全文浏览量: 345
- PDF下载量: 182
- 被引次数: 1